揚重作業の安全対策でお悩みですか?
揚重作業はすごくシンプルな作業です。
それにも関わらず、揚重作業で事故や物損が起こってしまうのはなぜでしょうか?
安全の話は重たく、小難しく、カタカナの専門用語が多いです。
なるべく難しい言葉は使わず、噛み砕いて 安全対策をご紹介します。
おそらく、この記事を見られる方は、
揚重に関わる企業のオピニオンリーダーか安全衛生責任者にアサイン(任命)された安全リテラシーの高い方ですよね。
大前提として、1つの安全対策で全ての事故を防げる便利な対策は存在しません。事故の要因は様々で、その要因1つ1つに適切な対応を取っていくことと、事前に予防することが必要です。
この記事では、揚重業界歴20年以上、揚重業界のリーディングカンパニーのケイ・マックスが行っている揚重作業の安全対策スキームをシェアします。
現場から、揚重作業の事故が少しでも減ることを祈っています。
それではTOC(目次)です。
揚重作業の安全対策が難しい理由
揚重作業の安全対策は難しいと言われてます。解体工事や躯体工事に比べても揚重作業は難しいとのことです。
その理由は揚重作業に以下の特徴があるからです。
- 新規入場の現場が多い(現場のルール・危険個所の把握の遅れ)
- 作業内容が日々変化する(特異な形状の搬入や、狭い搬入経路)
- 不定期に特殊環境での作業がある(高所、足場、雨天)
- 他職が関わってくる(他職への配慮がいきわたりづらい)
- 雇用期間が短い(安全衛生教育の効果が出にくい)
揚重作業はとてもシンプルで、材料を決められた位置に移動する作業です。それ故に、マニュアル化できない作業は個人の能力や判断による部分が出てきます。
例えば、搬入動線が1つではない場合もあります。
- 「差し上げ」か「階段揚げ」
- 「遠回りでフォークリフトで近づける」か「最短距離で台車で行くか」
どっちがより安全かの判断は、現場で行われ、他職との絡みや現場のルール等によって変わるため、1枚の手順書に網羅的に書くことはできません。
他には、作業者の能力によっても安全対策が違います。
例えば、Aさんはパネル4枚持って通れた通路が、Bさんは2枚でも難しいかもしれません。
また、搬入の難易度を見誤ったり、過信や省略行為、疲労による集中力の低下等のヒューマンエラーも関わってきます。
毎日同じ現場で、所定の位置で同じ作業(工場の様な)を行っていれば、手順書を作ってPDCAを回せば、事故は減っていくでしょう。
しかし、建設現場の特性上、毎回変化する現場環境等から安全対策は難しくなります。
揚重作業の安全対策上の3つの課題
建設業全般に言えることですが、現場の機械化や自動化があまり進みません。これは建設業が「人間主体」に構成されているからです。そして、揚重作業は人間主体で行う工程がほとんどです。人間の補助として設備・機器は進化していますが、建設業の主体が人間から変わるのはまだ時間がかかりそうです。
人間がもつ、柔軟性や多様性が揚重作業を的確かつ効率的にしている反面で、人間の脆弱な特性が事故を招く可能性もあります。ちょっと今、意識高いこと言いましたね。シナジーが生まれた気がします。
以下に、揚重作業の安全対策上の課題を挙げておきます。
- 作業手順書について、本来は作業内容の変化に伴い作業手順も適切なものに変更すべきです。しかし、変化する作業環境に対応する範囲には限界があります。理由は、同じ場所で、同じ条件で、同じ建築物は建たないため、標準の作業環境というものがないからです。そのため、安全対策のマニュアル化、標準化が困難となります。
- 多種多様な専門業者が同じ現場に入場し、それぞれの担当に応じて作業を進めるため、専門業者同士の連絡・調整を上手く図ることができない場合があります。
- 作業員の入れ替わりが多く、雇用期間も短い傾向があります。そのため、作業管理側も個々の作業員のクセや特性を把握しにくいです。また、継続的な教育や訓練を実施するのも難しくなります。
以上の通り、建設業界自体の構造や慣習の問題があり、課題自体の解消は難しいですが、課題を知ることで、対策が練りやすくなります。
揚重作業の安全対策の結論と概要
結論としては「組織全体で複数の対策を継続的に行う」ということになります。
ケイ・マックスの場合を図にすると以下のようになります。
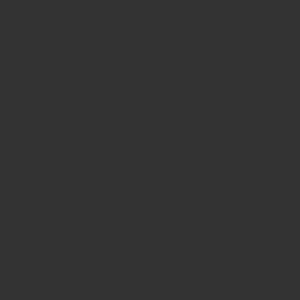
冒頭でも申し上げた通り、1つの安全対策で全ての事故を防止することはできません。ケイ・マックスでも、複数の安全対策が存在し、各々の立場で対策毎に相互にコミュニケーションをとっています。
形式的な安全対策や形骸化されている安全対策であれば、廃止するべきですが、安全は目に見えるものではなく、対策ごとの効果測定ができません。事故・ケガ・破損の件数など起きた事象の数でしか測れません。
安全対策の不足はだめですが、過度な安全対策も精神的な疲弊を招きます。現在でも、何がベストな安全対策かは社内でも議論が続いています。
個々の内容については、他の記事でも紹介しますが、特に作業員の安全意識の向上に効果的と思われるのが「KY活動・動線確認・荷姿」の報告です。安全意識の向上、作業員が主体的に安全活動を行う文化の醸成、安全に関わる現場教育・知識教育、現場管理者のフィードバックがあり、揚重作業の実務に沿った対策です。
動線確認とKY活動レポート
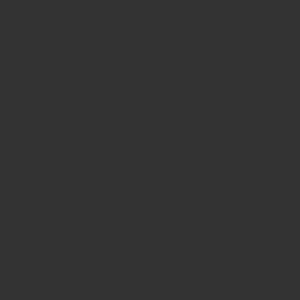
動線確認とKY活動は、現場では一般的なものかもしれません。
例えば、動線確認は搬入の前に搬入物が通る経路を事前に確認するわけですが、動線上に落ちている1本のビスを見て何を感じるかは、人それぞれです。
何も感じない人や、「踏んで刺さるかもしれない、滑って頭を打つかもしれない」と思う人、「必要なビスが抜け落ちてしまっているかもしれない」と職人に渡す人、「 クギを落とさないでくれ 」と職人へ注意する人など様々です。
この異なった現場の観方を、一定の安全水準まで高めるのが、動線確認と管理者からのフィードバックになります。現場管理者や安全管理部など現場を熟知した人の視点で、フィードバックを返すところまで行います。
また、「危険を予知するための前提知識の獲得」や「作業員本人が主体的に安全を考えるきっかけ」としての役割もあります。
KY活動レポートや荷姿の写真についても、同様の狙いがあります。
揚重作業-作業手順書-
冒頭で、揚重作業は作業手順書を作ることは難しいと言いました。
それでも、作業手順書があるのは、もし現場で何かのトラブルが起きた際の原因究明が簡単になるからです。
揚重作業と一口に言っても、扱う材料によっても対策が変わってきます。
「スチールパーティションの揚重作業」を例に作業手順書について書いていきます。
玉掛作業の安全対策については玉掛作業に係るガイドライン(中央労働災害防止協会-安全衛生情報センター)でまとめられていますので、ご参照下さい。
スチールパーティションの 作業手順書の例
ケイ・マックスには、以下の作業手順書があります。
左から「作業の手順」「予想される事故・災害」「リスクの評価」「事故災害防止(安全対策)」を定めています。
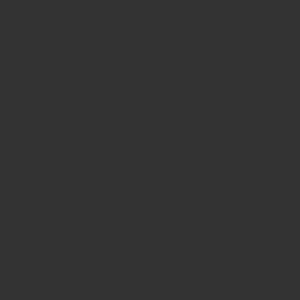
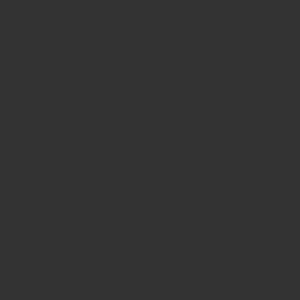
リスクアセスメントと作業手順の作り方
上の作業手順書はリスクアセスメント(アセスメント: 事前評価 )という手法に基づき作られています。 リスクアセスメントとは、現場の潜在的な危険性を事前に評価し、 除去・低減するための手法です。 リスクアセスメントはブリティッシュ(イギリス)の現場主体の安全対策をモデルとして、 2006年に日本でも労働安全衛生法にて 導入され、 努力義務となっています。
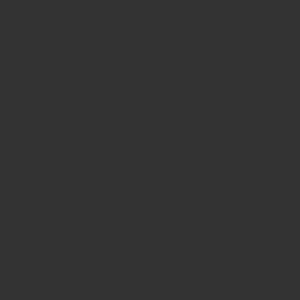
リスクアセスメントの進め方は以下の4つの手順に分かれます。
- 危険性の特定
- 危険性ごとのリスクの見積もり
- リスク低減措置
- リスク低減措置の実施
以降で見ていきます。
1.危険性の特定
危険性の特定は3ステップに分けられます。
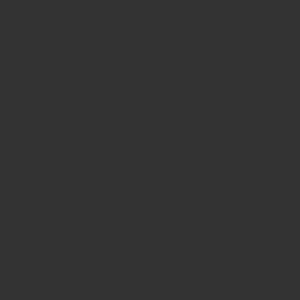
安全対策の担当者は、作業の工程ごとにすべての作業を対象とし、網羅的に危険性を特定し、発生の恐れのある災害を特定します。
STEP1:作業工程の洗い出し
まずは、下記の通り、揚重作業の情報を集めます。
全作業工程の情報を整理し、漏れなくダブりなく抽出しフロー図にします。
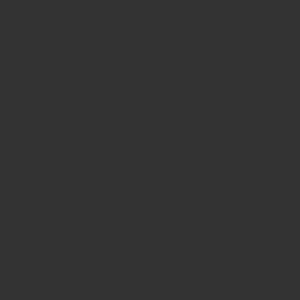
STEP2 危険性の特定
危険性の特定は、現場を熟知したベテラン作業員や現場管理者の着眼点を言語化したものを参考に、ピックアップします。
揚重作業の危険性を特定する為の着眼点です。
揚重する資材によって、細部は違ってくると思いますので、自社の場合に当てはめてブレインストーミング(アイデア出し)して下さい。
- 鋭利な箇所・材料(小口・バリ)はないか。
- 開口部はないか
- 頭部を打つような箇所はないか。
- 滑ったり、つまずいたりする箇所はないか。
- 昇降する場所から落下する危険はないか。
- 感電するような箇所はないか。
- 揚重設備(EV、ハンドリフト、台車 等)の駆動部、回転部に手・指は、はさまれないか。
- 作業姿勢を極端にする箇所はないか。
- 動線上の他業種、第三者への接触の可能性はないか
- 材料の置き方や置場により、荷崩れは起きないか
- 危険物による爆発・火災などの災害、および有害物の被ばくなどによる健康障害が発生する物質を周囲で使用していないか。
- 誤作動、または不意に作動する機械・設備はないか。
- 作業環境は整っているか。
- 災害時(地震、火災など)の対策はできているか。
さらに、日頃行っている安全パトロールや危険予知活動、過去の災害・事故事例などから把握される危険性についても記載します。
STEP3:予想される事故・災害の特定
特定された危険をもとに、その危険がもたらす事故・災害を特定します。
2.危険ごとのリスクの見積り
出された危険性を元に、リスクを評価します。
リスクの見積もりは、マトリクス(表)によって行います。現場を熟知するリーダーが複数集い、多数決ではなく合意を得ながら評価していきます。
リスクの見積もりは、「重大性」と「起こる可能性」を軸とし、〇=0.5、△=1.5、✖=2.5で評価します。
可能性\重大性 | 軽微 (不休災害) 〇 | 重大 (休業災害) △ | 極め重大 (死亡・障害) ✖ |
ほとんど起こらない 〇 | きわめて小さい 〇〇→1 | かなり小さい △〇→2 | 中程度 〇✖→3 |
たまに起こる △ | かなり小さい △〇→2 | 中程度 △△→3 | かなり大きい △✖→4 |
かなり起こる ✖ | 中程度 ✖〇→3 | かなり大きい ✖△→4 | きわめて大きい ✖✖→5 |
3.リスク低減のための優先度の設定・リスク低減措置内容の検討
上の表では、リスク=発生の可能性×重篤度でリスクを見積もりました。 下の表で、リスクの点数を元に、安全対策の優先度を決定します。
リスクポイント | 優先度 | |
5-4 | 高い | 直ちにリスク低減措置を講ずる必要 措置を講ずるまで作業停止、十分な経営資源を投入する必要がある |
3-2 | 中 | 速やかにリスク低減措置を講ずる必要あり。 措置を講ずるまで、作業停止が望ましい優先的に経営資源投入 |
1 | 低 | 必要に応じてすぐ低減措置を実施 |
4.リスクの低減措置の実施
上記3.のマトリクス(表)により、プライオリティ(優先度)を決定したら、リスクへの対策を行います。
対策にも順序があり、以下の①~④のようになります。
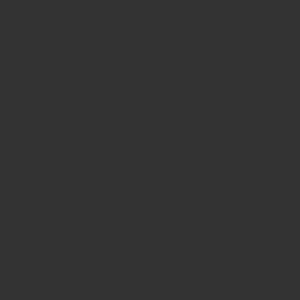
上図の①と②は「建築物の設計」や「ロングリフトエレベータの安全バーが閉まらないと動作しないインターロック(特定の条件がそろっていないと動作しない仕組み)」の話なので、専門工事業者や1次、2次下請けが主体的に行える安全対策としては現実的ではりません。
そのため、上図③のマニュアル・作業手順書、教育訓練などの管理的対策と 上図④保護具の検討が現実的なラインです。
揚重作業の安全対策-ヒューマンエラー対策
ヒューマンエラー(人的ミス)を0にするのは人間の特性上、不可能です。完全な手順書を作り、完璧な保護具があったとしても、人間のミスがある以上、事故は起こってしまいます。
このエラーが起きる影響をコントロールするのが、ヒューマンエラー対策です。
弊社の安全管理部の情報よると、揚重作業の事故の6割がヒューマンエラーだそうです。これは、手順書や安全保護具などの管理的対策以上にヒューマンエラーが多いという事です。
揚重作業におけるヒューマンエラー8種類と対策
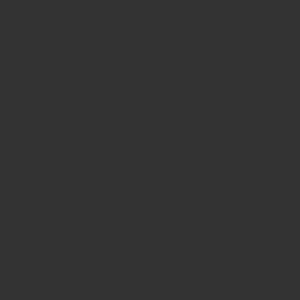
8種類のヒューマンエラーについて、揚重作業を例に見ていきます。
少し長いですが、参考にされてみてください。
無知、未経験不慣れ
未経験の作業員は、現場のどこに危険が潜んでいるか分かりません。また、ベテランであっても初めて扱う材料や、初めての現場もこのヒューマンエラーは当てはまります。
・揚重作業に不慣れな作業員が、吊り荷の下に入って入ってしまう。
・熟練の作業員が、初めての現場で立ち入り禁止区域を知らずに、開口部に落ちる
対策は、知識・技術の教育、個人の運搬能力に合わせた適正な人員配置があげられます。
弊社の場合は、新人作業員がいると、ベテラン作業員がマンツーマンでついて、直接教育します。
また、現場を熟知した作業管理者が、作業員の性格や技量を考慮した適正配置を行っています。
危険軽視、慣れ
ベテラン作業員が十分な現場経験があるため、慣れによって安易な行動をすること等が危険軽視に当たります。
いくら「油断するな、危険を軽く見るな」と口を酸っぱく言っても、本人への浸透には限界があります。現場の職長など、現場に近い人の監視が大きな影響を持ちます。
対策としては、危険軽視に対して、きちんと注意し是正できる管理者を置くこや、良好な人間関係の形成などにより、後腐れなく、自主的に安全意識を育むよう言っていくことが挙げられます。
不注意・疲労・単純作業による意識の低下
雨天時の搬入などで、集中力が下がり注意散漫が要因となり、ヒューマンエラーが起こります。
人間の特性として、1つのことに集中すると、他のことは不注意になります。
例えば、足元が悪く下を向いたまま搬入をしていると、角で人と接触するのが不注意に当たります。
対策としては、不注意が起きても事故に繋がらない様に対策を練ることです。
作業前に事故につながる要因を予め発見するべく、導線確認を行い、邪魔なものを取り除く等の設備の対策が挙げられます。
連絡不足
安全指示が、うまく伝わらないことによるヒューマンエラーも起こります。いつも行っているからと作業指示がなかったり、マンネリ化して、本来伝えるべき内容が伝わっていないこともあります。
「指示の内容があいまい」「指示をきかない」「指示の内容を理解していなかった」という
作業を指示する元請け側も指示し忘れも起こりえます。
例えば、現場のルールで繊細なクロスの素材で仕上がった壁の現場で「ヘルメットをかぶらない」という特異なルールはたまにあります。
対策としては、安全指示をする側が、作業員の技量・クセ・性格を把握することと、相手の安全知識を考慮した言葉選びを行うことが挙げられます。また、出した指示が守られているかどうか、目視で確認することが挙げられます。
集団欠陥
元請け会社の工期に余裕がなく、依頼に応えようとし不安全行動が起きたり、不安全行為を注意しずらい雰囲気になることがあります。無言の「空気読め」の強要という状態が集団欠陥です。1次、2次の関係性や、先輩、後輩の関係上、職務上の関係から不安全行動を指摘できないことが起こります。
対策として、個人で現場の空気に立ち向かうことは難しいため、組織的な対策が必要になります。発注段階における適正工期の検討や、現場の異常な雰囲気に気付いた作業員が作業管理者に報告しやすい雰囲気づくり、現場の雰囲気から離れた番頭さん同士による工程管理の検討等が考えられます。
近道・省略行動本能
人間には、近道したい、面倒な手順を省略したいなど、効率的に作業を進めたい本能があります。立馬を使わないといけない状況で手元にある脚立を使う、安全通路をショートカットする場合が近道、省略行動本能に当たります。
対策としては、近道行動が起きないように作業通路を設計することなど省略行為ができないように設備面での対策や、横着行為をしなくて済むように事前に作業準備を完璧にしておく等が挙げられる。
パニック・場面行動本能
パニックは、自分の処理能力以上の作業内容を与えられたらり、、切迫した状態で一時的に正常な判断ができなくなる状態を言います。
場面行動は、「注意が1点に集中し、周りを見ずに行動してしまう本能」の事を指します。例えば、足場からラチェットを落としそうになり、とっさに身を乗り出すのが、場面行動本能に当たります。
反射的に起こってしまうため、反応事態を止めるのは極めて困難です。
対策としては、焦りや緊張が生まれる職場環境(急かさない、煽らない)を作らない、複数の作業内容がある場合は、指示する側が紙などに整理して渡す等です。ようは、ゆっくりと落ち着いて危険に注意を向け続けれる状態を作ることが挙げられます。
錯覚・思い込み
勘違い、先入観、思い込み、見当違い、自分の経験・知識の過信がこれに当たります。台車の耐荷重を誤って認識していた、
特に、新規の現場では、以前の現場と違う設備や運用があり、思い込みが起きやすくなります。
対策としては、行動へ移す前にもう一度確認する、自分の判断や評価が間違っていないか相談する、要所での注意喚起を促す、判断基準を明確化する、などが挙げられます。
まとめ
1つの安全対策で、全ての事故を防ぐのは難しく、組織全体で安全対策を行っていく必要がある。揚重作業は標準作業の環境設定ができず、安全対策は難しい。作業手順書はリスクアセスメントを元に作れるが、全ての作業を網羅できない。揚重作業の事故の多くはヒューマンエラーが関わっており、ヒューマンエラーに対しては、個別に対策する必要がある。
以上のように、安全に対する考え方をご紹介しましたが、あくまで対策の一つとして考えていただければと思います。この記事もそうですが、知識や運用は現場で活かされないと、何の意味もありません。
安全対策が有効に働くには、組織が一体となって作業員への理解と、現場管理者の地道で粘り強い指導が必要かもしれません。
そして、安全対策自体も「100%の安全はない」という意識のもと、常にアップデートし続けなければいけない分野かもしれません。